AR is driving the next step of digitalisation in the industrial workplace
Augmented reality is becoming an integral part of industry 4.0 initiatives and the emerging industrial metaverse – driving future competitive advantage and delivering real value through process efficiency, improved collaboration and sustainability benefits.
Beyond the consumer metaverse hype, industry-proven, fully integrated AR solutions are already helping companies do more with less, empower their employees and serve their customers more quickly and efficiently.
Streamlined processes – greater efficiencies
AR streamlines manual processes and improves collaboration in the industrial workplace by assisting workers with AR-enabled guides & instructions and by connecting frontline workers with remote experts for see-what-I-see support.
AR can overlay step-by-step work instructions onto the physical world, and head-mounted AR displays allow hands-free working. Easier access to critical information speeds up processes, decreases error rates, saves costs and improves safety and ergonomics.
Focus on concrete use cases with people first
We offer AR-powered connected working solutions that build upon your existing digitalisation efforts and enhance the work your employees are already doing in assembly, manufacturing, maintenance and logistics. We help you identify concrete use cases with an opportunity for quick wins to build confidence and buy-in – and assist you all the way from pilot implementation to deployment and scaling.
We emphasise a human-centered approach. The objective is to give your workers better digital tools to allow them to be more effective in a safe workplace. For you, this means a more engaged, committed and adaptive workforce.
Industry-proven solutions from our world-leading partners
We are proud to partner with world-leading AR platform and hardware vendors with innovative, industry-proven technology. Thanks to our strong partnerships, we have the right resources and capabilities in place to deliver solutions and services in an agile and efficient manner.
Find out more about the partners we work with.
At your service, every step of the way
These are the key steps we follow to ensure that every project we deliver is a success.
Consulting & scoping
By understanding your needs and goals and drawing on our expertise in lean management, we evaluate where it makes business sense to support your workers with industrial AR solutions. We then identify a concrete use case together with you.
We also assist you in scoping the project and selecting KPIs to gauge the performance and success of the project.
Configuration & customisation
Whilst the solutions employ self-service tools to quickly create and update workflows with easy drag-and-drop functionalities, build processes from scratch, customise templates and more – with no programming skills – we are ready to help you in configuring and customising the solution for you.
Piloting & implementation
We help you with the technical implementation, assist in choosing the right hardware and organise training tailored to the needs of your operation and workers. We also assist you in integration to your backend systems and provide the support needed for a frictionless roll-out.
If you decide to start with a pilot implementation, we support you in setting up and completing the pilot.
Service & support
We collaborate with you to draw up a service agreement that makes sense for you and fits the level of support you need. The remote support capabilities of our partners mean assistance can be provided instantly.
Industrial AR solutions are quick to deploy, easy to integrate to backend systems and intuitive to use. Let’s get started! We’re here to help.
NIKO SILTAKORPI
Customer Success Manager
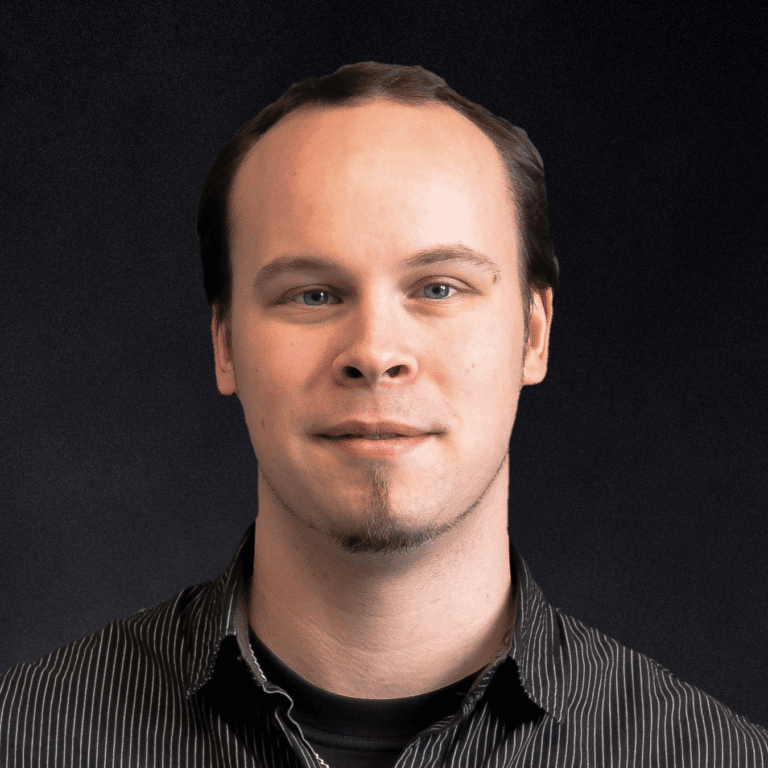
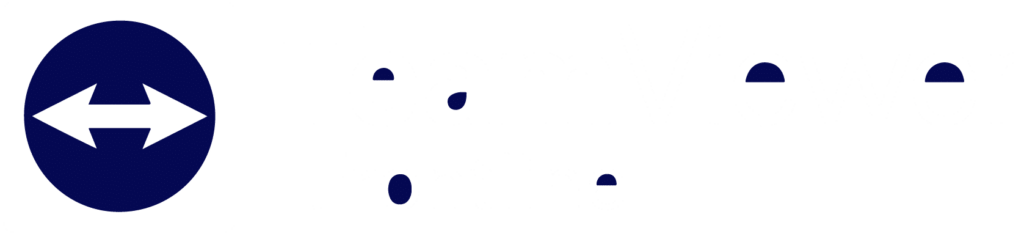
All-in-one AR platform for productivity gains, cost savings and more satisfied employees
TeamViewer Frontline is a suite of industry-proven AR & MR solutions for optimising manual work processes and speeding up onboarding and training in industrial environments.
The solutions are built around the needs of frontline workers: Hands-free access to clear step-by-step instructions, instant remote assistance and self-paced learning-by-doing enhance worker performance and boost job satisfaction. You obtain more efficient and resilient processes with shorter downtimes, reduced error rates and improved safety.
The platform is highly flexible in terms of employee skill levels and language needs, and it is endlessly configurable – meaning you can quickly customise solutions to meet your needs and use cases. Scalable implementation, easy integration into backend systems and a no-code approach ensure rapid time to value.
TeamViewer Frontline solutions support workers and increase productivity on the shop floor, in warehouses and in the field. Take a closer look at the solutions.
xPick for logistics and warehousing
TeamViewer Frontline xPick is a proven, market-leading vision picking solution that is in use in large-scale implementations worldwide. In combination with smart glasses, xPick offers a strong alternative to handheld scanners and paper lists to support manual order picking, inventory control, and most other logistics processes.
Working hands-free means your employees can perform tasks quicker and with fewer errors. The intuitive graphical interface ensures quick implementation and acceptance, and optional components – including weight control, barcode scans, localisation and voice command – broaden the range of possible applications.
xMake for assembly and production
TeamViewer Frontline xMake allows you to easily digitise assembly and manufacturing instructions and standard operating procedures and bring them on smart glasses and other wearable devices. All relevant information and instructions are displayed right in the worker’s field of view. Voice commands, sensors, or image recognition let workers pull up the necessary data, while keeping their hands free for the task.
The dynamic step-by-step instructions and rich multimedia information – including text, graphics, images, video and audio – help workers carry out their tasks faster and with less errors. Cameras and sensors provide a standard quality assurance system that ensures perfect results and documentation.
xInspect for inspection and maintenance
TeamViewer Frontline xInspect is an innovative “inspect-by-vision” solution that digitises your manuals and pairs with smart glasses so that all relevant information – like guidelines, checklists, visualisations, circuit diagrams, etc. – are always right in the line of sight without compromising on a workers’ mobility. In case onsite technicians cannot resolve a problem, the built-in remote assistance functionality helps to significantly reduce machine downtime and expert travel costs.
You can also shorten training times and onboard new employees more efficiently with the rapid knowledge transfer enabled by xInspect. And with clearly visible hazard warnings, work becomes safer.
xAssist for remote assistance
TeamViewer Frontline xAssist takes knowledge sharing to the next level, enabling remote experts to provide real-time augmented reality support for field service technicians from anywhere, anytime. Onsite technicians can send accurate visual information to technical support and receive troubleshooting and other expert help directly from their smart glasses – hands free for the task. Live pointer and annotations help clarify information.
Experts are hard to find and bringing them onsite is costly. With xAssist, experts can share their expertise cost-efficiently, instead of wasting time on travel, whilst frontline technicians can solve issues faster and offer a better service experience for customers.
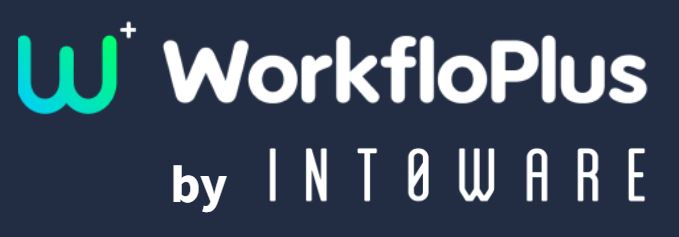
Transformative digital platform that ensures standardised, repeatable and auditable processes
WorkfloPlus is a SaaS digital work instruction solution that converts and enhances existing paper-based and human processes into easy-to-follow, step-by-step digital work instructions.
An online management portal allows you to quickly download & update workflows and then roll the new processes out across your team in an instant. So you can be sure everyone always works to the latest way of carrying out a job – all with an automatically generated audit trail for compliance.
Instant reporting provides an accurate real-time view of operations in the field and generates detailed information for data-led decision making and continuous improvement. The solution is accessible via mobile, wearables and desktop devices and easily integrates with your existing technology.
Intoware’s WorkfloPlus boosts productivity, improves communication and guarantees compliance across industries and functions. Find out more about the use cases.
Compliance & assurance, auditing & reporting
WorkfloPlus is an excellent tool for external audits with photo and video evidence to show exactly what took place and prove compliance adherence. Easy-to-follow digital instructions help complete quality checks, and instant sharing of information with customers improves communication and satisfaction levels.
With instant updates and version control, you can keep up with regulatory changes and quickly roll out up-to-date work procedures across the entire team – so you can be sure that frontline workers are always using the latest compliant instructions. The platform also enables you to track employees’ qualifications, certifications and training records, so only qualified personnel perform critical tasks, reducing the risk of errors and non-compliance.
Assembly & installation, maintenance & repairs
WorkfloPlus speeds up assembly, installation and maintenance, enhances safety and increases visibility. Step-by-step instructions provide clear guidance, and removing the need to manually enter paper-based logs into centralised systems eliminates information delays. Connected workers can instantly submit data and notify backend teams.
Using paper forms and checklists to record snagging lists, obtain customer sign-off and conduct onsite health & safety checks is time-consuming and open to errors. WorkfloPlus removes the room for error with digitised checklists and workflows. Capturing the exact time and attendance of procedures – including photo uploads for audit trail purposes – enhances visibility and improves customer experience.
The dynamic step-by-step instructions and rich multimedia information – including text, graphics, images, video and audio – help workers carry out their tasks faster and with less errors. Cameras and sensors provide a standard quality assurance system that ensures perfect results and documentation.
Health & safety
WorkfloPlus reduces the chance of workplace injuries by offering step-by-step guidance, taking workers through risk assessments and safety audits, and making sure the right equipment and processes are always used.
Health and safety procedures, compliance and audit checks are often frequent and detailed and create a massive volume of paper, which is difficult to track. With WorkfloPlus you can ensure all your safety procedures, inspections & equipment checks are carried out correctly, at the right time and with auditable data recorded throughout the process.
Training & knowledge transfer
WorkfloPlus allows you to capture any process and record it digitally – including the knowledge, techniques and tried-and-tested methods that experienced workers have created themselves to carry out tasks more efficiently. The insight and expertise they’ve accumulated over the years and stored in their minds can be translated into digital instructions and processes to support with onboarding, training and upskilling and accelerating knowledge transfer to the next generation of workers.
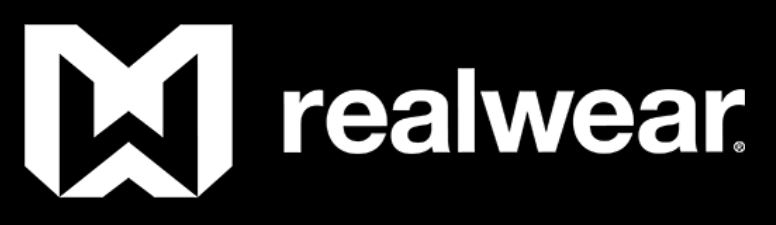
Assisted reality wearable solutions that keep your frontline workers safe, protected and productive
RealWear is the world’s leading provider of assisted reality (aR) wearable solutions. It has become the gold standard to engage, empower and elevate frontline professionals to perform their work tasks more safely, efficiently and precisely. Using head-mounted RealWear devices, workers can access and view equipment manuals, multimedia files, complete documents and remotely collaborate with offsite experts in real-time – while keeping their hands and field of view free for work.
The voice-controlled headsets are designed for industrial environments. They are ruggedised, durable and compatible with PPE, like hard hats and eyewear. The high-resolution micro displays are slim to maintain field of vision but are also adjustable to be moved out of the wearer’s view.
RealWear is field-proven in a wide range of industries with thousands of world-class customers. Learn more about the different use cases.
Remote expert guidance & visual assist
Using video collaboration applications with RealWear, frontline workers can easily connect with experts, other team members or partners and clients in real-time – from anywhere – for troubleshooting, equipment repair, audits, approvals, training and other mission-critical tasks. Remote experts can see what the worker is seeing, provide guidance, push relevant documents to the worker’s display and place annotations on the shared view.
The RealWear devices are equipped with a high-definition camera for capturing photos and videos in hard-to-reach places like tunnels, towers, or behind large machinery and equipment, allowing frontline workers to leverage the devices for hands-free verification and visual documentation.
Digital workflow
Digital workflow solutions support frontline workers by providing visual instructions, checklists, data entry, and visual documentation of completed steps while on the go. RealWear devices enable digital workflows to reach workers when and where needed – directly in the field of view – improving productivity and reducing operational errors.
Document navigator
RealWear devices allow frontline workers to view technical manuals, installation instructions, construction drawings, wiring diagrams, exploded view drawings, safety procedures and other critical information with eyes forward and hands free. QR codes attached to physical assets can be scanned by the device camera to bring up the right document in the right place – reducing the time spent searching for the right information. Voice-driven zoom and head movements for panning ensure an intuitive user experience.
Industrial IoT data
To carry out performance monitoring, diagnostics and predictive maintenance, a field worker may need real-time access to current and historical data generated by equipment sensors. RealWear devices can access the network to provide the worker with such contextual and actionable IoT data, based on equipment location, name or number.
Read more about accelerating productivity and generating ROI with RealWear solutions.

The Realwear Thermal Camera Module is a new hardware offering that builds on the promise that RealWear made with the launch of the RealWear Navigator 500 to provide a truly hands-free, modular solution for the complex needs of our customers. It is compatible only with the Navigator 500 series, and it’s available to order starting today. It offers the ability to switch seamlessly between viewing the visible and infrared spectrums so that you can spot issues before they become problems.
With the RealWear Thermal Camera Module, you can ‘see the invisible.’ It has a dual-camera unit to provide the ultimate hands-free thermal experience.
Benefits
Hands free
Perform an inspection or diagnose an issue hands-free using your voice, helping you be safer & more productive.
New Perspectives
With thermal and visible sensors, you can see what you can’t see with the naked eye. Spot issues before they become a problem.
Built to Last
Maintains ruggedness and IP66 rating so you can keep using your Navigator even in dusty or damp environments.
Use cases
Motors and Pumps
Great for process checks. Can perform line inspections, diagnose machinery overheating or friction in bearings, and more.
Electrical Inspections
Diagnose potential areas for preventative maintenance or repair by identifying spots exhibiting out of ordinary temperature.
Building Diagnostics
Identify areas with missing insulation or air leaks. These areas will show up as cold or hot spots relative to the surrounding area
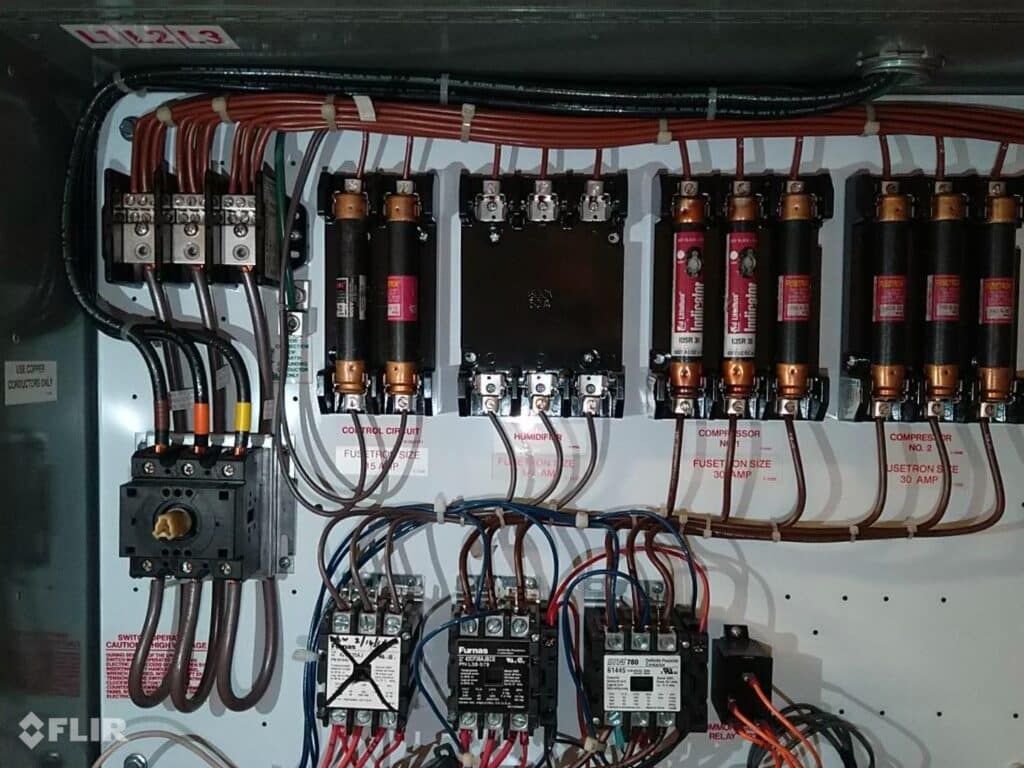
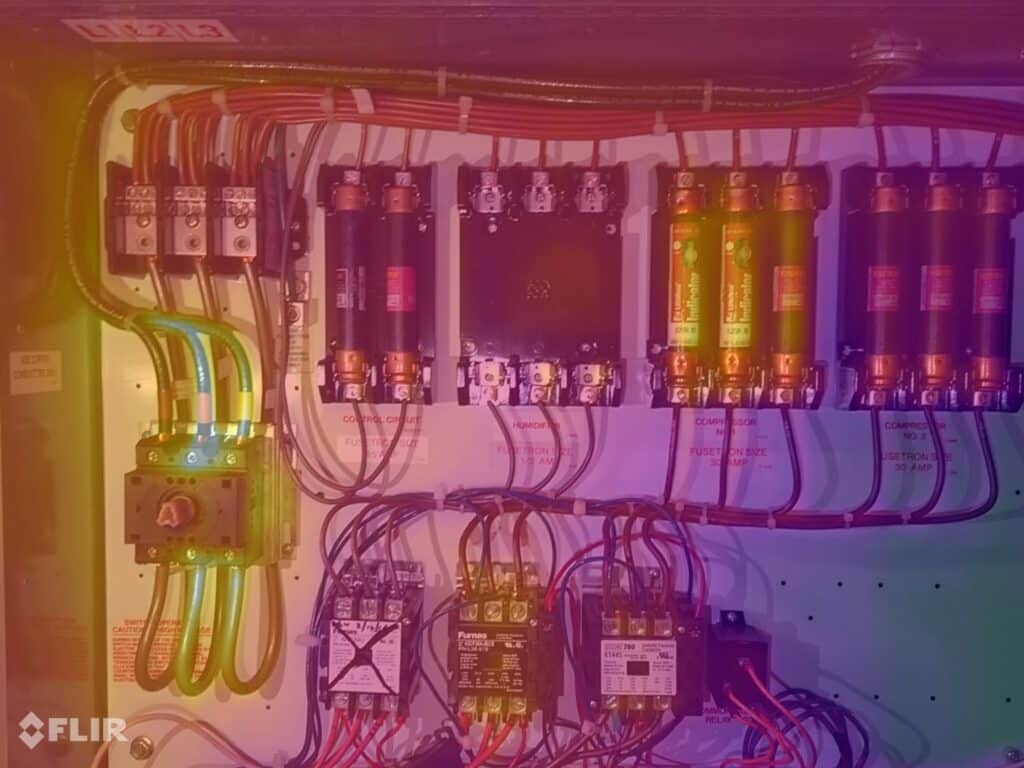
