Need for on-the-job guidance
It was June 2011. I was starting my summer internship in one of the leading automobile manufacturing firms in South Asia. My initial task was to observe bus body parts – what were those parts, how were they being assembled and were there any abnormalities in the overall docking process (assembling the bus body with the chassis).
In the first few weeks, I was completely confused. I could not tell one bus model from another, let alone the bus body parts, overall process steps and docking process. I spent the first three months of my four-month internship just trying to understand the overall process, bus model numbers and their respective parts. It was only in my fourth month that I was able to give some concrete suggestions related to process improvements. When I went back to the university, I was not surprised to hear many of my coursemates complain that they could have done so much more, if only there had been more time.
Typical training periods in the automobile and other industrial sectors range from four to six months and even then, there is no guarantee the trainee is ready to start as a fully-fledged production worker on a manufacturing line or prepared to work independently on service & maintenance tasks in the field. The larger the original mismatch between worker skills and work content, the more time and money is needed to bring employees’ skills up to speed.
Enterprise augmented reality
There is no magic pill solution for the skills gap and all the new skill demands that new employees face, but if we were to compare existing and emerging solutions in terms of effectiveness and time to implement, step-by-step instructions in augmented reality would be one of the best solutions in many situations.
Augmented reality in itself is a vast field, consisting of various technologies such as markerless AR, marker-based AR, location-based AR, spatial recognition and object recognition. These technologies help people make better sense and use of data by visualising any data directly on real products, equipment or environments. Read our blog post on “Augmented reality in corporate training“ to learn more about AR.
With stronger hardware and better algorithms, AR technology is developing at a greater pace than ever. ARKit and ARCore are packed with various features, specifically for the B2C segment, whereas platforms like Vuforia focus on industrial AR applications. Among the latter, there is an AR tech supplier with its services spanning the product lifecycle. RE’FLEKT GmbH and its enterprise AR ecosystem – with best-in-class object recognition, cross-device support and an easy to use authoring tool – check all the boxes of a plug and play AR solution for industrial applications.
REFLEKT ONE for step-by-step instructions in AR
RE’FLEKT’s AR solution for step-by-step work instructions is called REFLEKT ONE, which is supported on iOS, Android and Windows platforms, like HoloLens. REFLEKT ONE consists of three main elements:
- Authoring to create AR content from technical documents, CAD files etc.
- Publication and hosting of AR content on the Azure cloud or in the customer’s IT environment
- Visualisation of the AR content on any mobile device or smart glasses
How does REFLEKT ONE assist workers once the solution is implemented?
Let’s think of a use case: There is an industrial grade large electric motor that requires repair. A field service technician reaches the premises. He takes out an iPad, scans a QR code on the machine to find out the model number from REFLEKT ONE viewer client and within seconds, he sees an augmented version of the necessary repair steps on his screen:
Step 1. Please remove the right-side cover
This highlights the exact part that needs to be removed with screws around it.
Step 2. Please remove the rotors
The rotors are highlighted, and an AR animation explains how to remove them.
The AR-based guidance continues with the next steps.
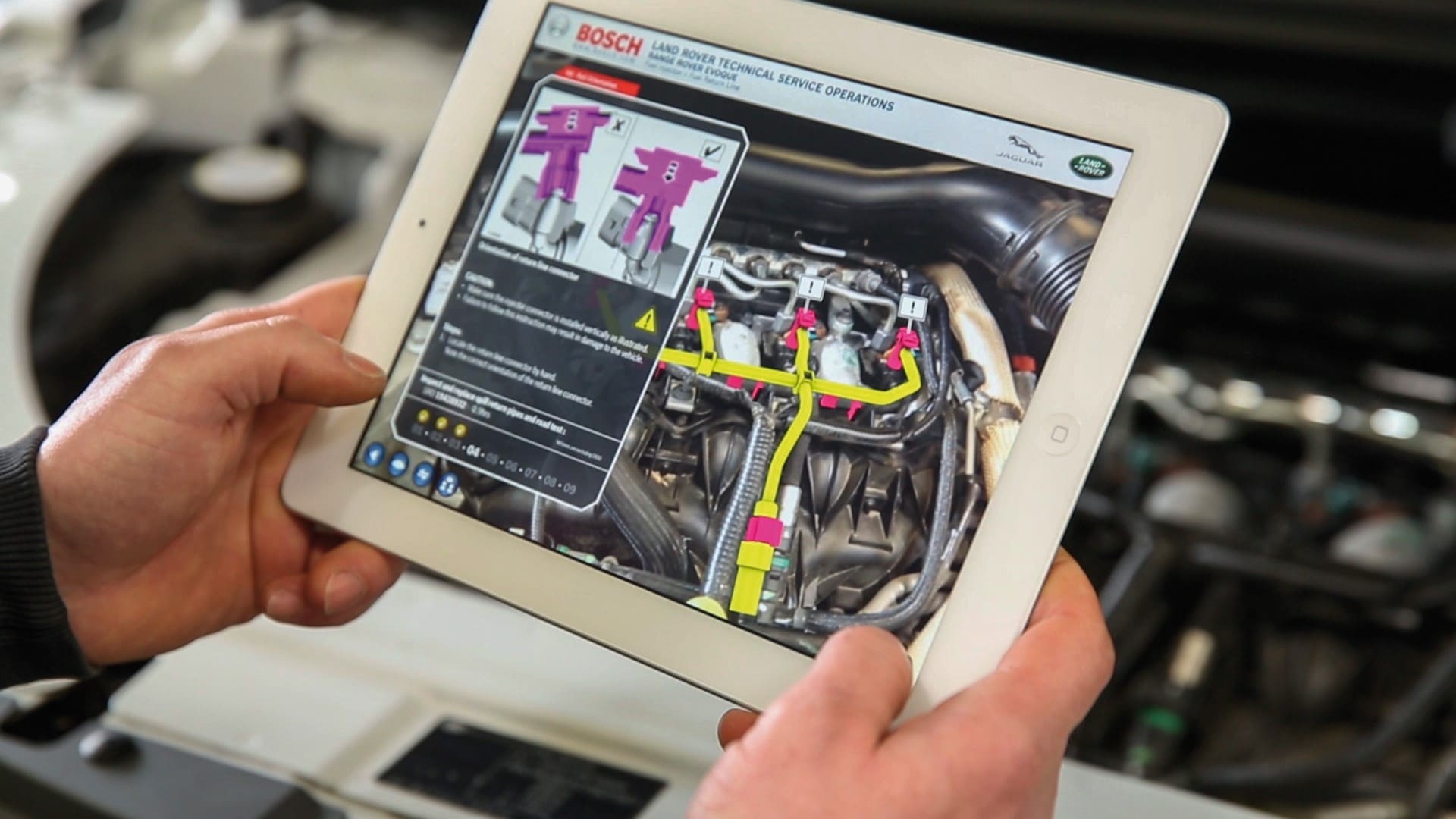
The direct benefits of such AR-assisted work include
- Control over the work process – higher first-time fix rates, consistency and high quality maintained
- Effective on-the-job knowledge transfer – less experienced workers able to complete the job
- Up to 30% faster work with on-demand, in-context information – shorter downtimes, higher productivity
Using wearable technology, AR-powered smart instructions can be displayed in the workers’ field of vision, freeing up their hands and gaze for the job. For even more effective on-the-job or guidance, REFLEKT ONE can be combined with REFLEKT Remote, an AR-based solution that connects field workers to a remote expert in one simple click.